私たちの生活を支える様々な工業製品の製造に欠かせない超硬合金は、硬度がダイヤモンドに次ぐとされ、高温での加工や長時間の使用にも耐える特殊な素材です。
今回は、この超硬合金について、基礎から応用まで分かりやすく解説していきます。
超硬とは
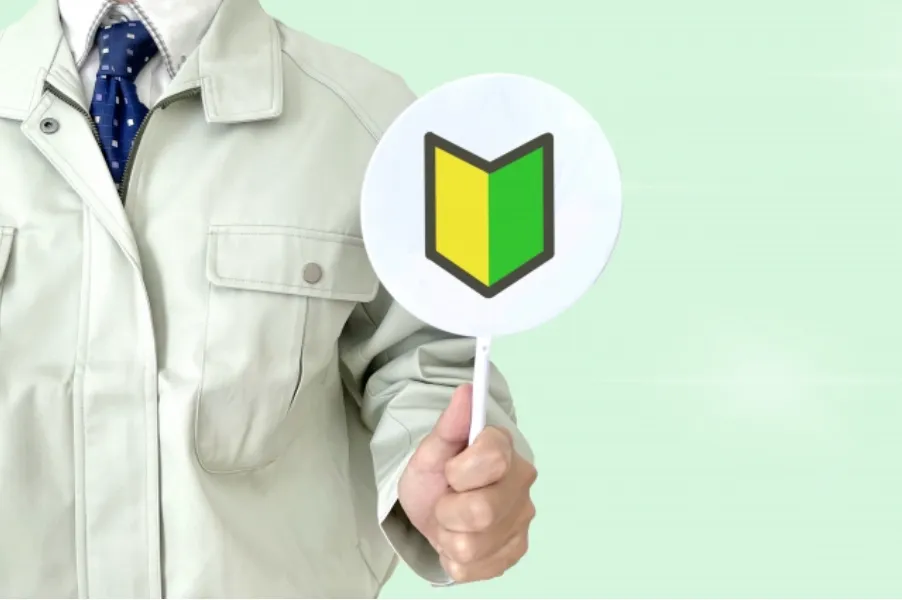
現代のものづくりに欠かせない超硬合金は、その名の通り非常に高い硬度を持っています。ダイヤモンドに次ぐ硬さを誇るこの素材は、切削工具や金型など、様々な産業で活用されています。しかし、「超硬」と「超硬合金」の違いや、他の金属との区別について、正確に理解している人は少ないのではないでしょうか。
ここでは、超硬の基本的な定義から、他の材料との違いまでを詳しく解説します。
定義
超硬合金は、タングステンカーバイドを主成分とし、コバルトなどの結合材を混ぜ合わせて1400度前後の高温で焼き固めて作られる合金です。
この製法により生まれる独特の性質は、一般的な金属材料では実現できない高い硬度と耐熱性を実現し、切削工具や耐摩耗部品として広く活用されています。また、材料の配合比率や粒度、焼結条件を変えることで、様々な特性を持つ超硬合金を作ることが可能です。
用途に応じて最適な性能を発揮する材料設計が可能となり、現代の製造業における不可欠な素材として確固たる地位を築いています。
超硬合金とも言う?
「超硬」という略称で知られていますが、正式名称は「超硬合金」です。これは英語では「cemented carbide」や「tungsten carbide」と呼ばれ、硬質の金属炭化物と金属バインダーを組み合わせた複合材料であることを示しています。
製造方法や組成から見ても、単なる硬い金属ではなく、特殊な合金として扱われるべき材料といえるでしょう。
名前の違いは、単なる呼び方の問題ではなく、その材料特性や製造プロセスの特殊性を表現しています。特に工業分野では、その性質や用途を正確に伝えるために「超硬合金」という正式名称が使われ、材料の特性や品質管理において重要な意味を持っています。
サーメットとの違い
超硬合金とサーメットは、どちらも金属とセラミックスの複合材料ですが、その主成分が大きく異なります。
超硬合金がタングステンカーバイドを主成分とするのに対し、サーメットは炭化チタンや窒化チタンが主成分です。この成分の違いは、材料の特性に大きな影響を与えます。例えば、超硬合金は高い硬度と優れた耐摩耗性を持つ一方、サーメットは耐熱性に優れ、より高速での切削が可能という特徴があります。
また、製造コストの面でも違いがあり、希少金属であるタングステンを使用する超硬合金は、比較的入手しやすいチタンを使用するサーメットと比べて製造コストが高くなる傾向があります。
タングステンとの違い
純タングステンと超硬合金は、しばしば混同されますが、全く異なる材料です。
タングステンは単体の金属元素で、主に電球のフィラメントなどに使用される一方、超硬合金はタングステンカーバイドとコバルトを組み合わせた複合材料で、工具や金型などの工業用途に特化しています。タングステン単体は非常に高い融点を持ち、電気伝導性に優れる特徴がありますが、加工が難しく、もろい性質があります。
これに対して超硬合金は、結合材であるコバルトの効果により、高い硬度を保ちながらも適度な靭性を持ち、工具材料として理想的な特性といえるでしょう。
超硬合金の特徴

超硬合金は一般的な金属材料とは全く異なる特性を持っています。その最大の特徴は、高温下でも安定した硬度を維持できることです。また、熱による寸法変化が小さいことも、精密加工には重要な利点です。
ここでは、超硬合金ならではの特徴について、実際の使用場面に即して解説していきます。
硬度が非常に高い
超硬合金の最大の特徴は、その名の通り非常に高い硬度を持つことです。
ダイヤモンドに次ぐ硬さを誇る超硬合金は、タングステンカーバイドの結晶構造に由来し、1400度という高温での焼結過程で形成されます。
この特性により、高速切削や連続加工などの過酷な条件下でも安定した性能を発揮できるのです。
熱膨張率が小さい
超硬合金は、熱による寸法変化が極めて小さいことが特徴です。
一般的な金属材料と比べて熱膨張係数が小さく、これは精密加工において重要な利点です。例えば、高速切削時に発生する熱で工具が膨張すると加工精度が低下しますが、超硬合金製の工具では熱による寸法変化が最小限に抑えられます。また、金型材料として使用する場合も、温度変化による寸法変化が少ないため、高精度な成形加工が可能になります。この特性は、特に電子部品や医療機器部品など、高い寸法精度が要求される製品の製造に大きく貢献しているといえるでしょう。
超硬合金の種類
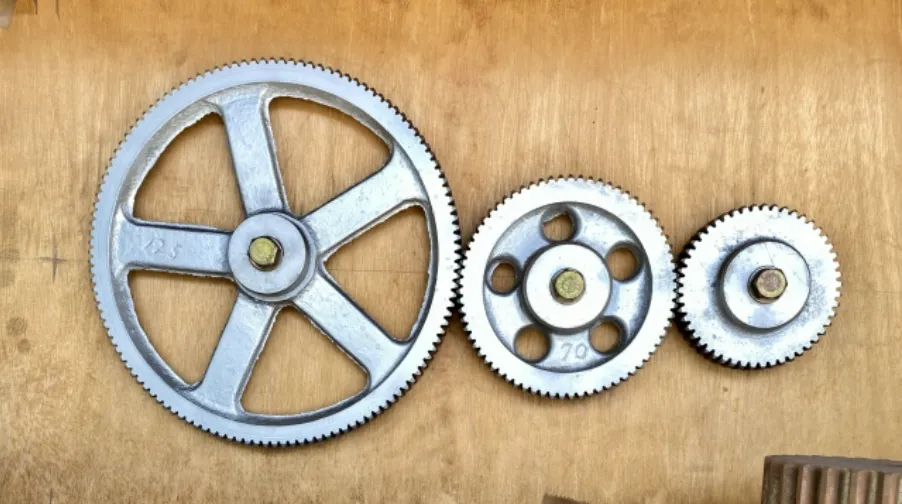
超硬合金は、用途に応じて異なる組成や特性を持つ種類が開発されています。主にP種(鋼用)、M種(汎用)、K種(鋳鉄用)の3種類に大別され、それぞれが特徴的な性能を発揮します。
ここでは、各種類の特徴や適した用途について、実際の使用例を交えながら詳しく見ていきましょう。
P種
P種は鋼用超硬合金として知られ、主に鉄鋼材料の加工に使用されます。
タングステンカーバイドに加えてチタンカーバイドやタンタルカーバイドを含有させることで、高温での化学的安定性を高めています。この特性により、鉄との親和性が低く、切削時に工具が損傷しにくいことが特徴です。特に連続切削作業において優れた性能を発揮し、自動車部品や産業機械部品の製造ラインで広く使用されています。
また、耐クレーター摩耗性に優れているため、高速切削や長時間の連続加工にも対応可能で、生産効率の向上に貢献しています。
M種
M種は汎用超硬合金として位置づけられ、P種とK種の中間的な特性を持っています。
様々な被削材に対応できる多目的な合金として開発され、ステンレス鋼や耐熱鋼、チタン合金などの難削材の加工に適しています。結合材として使用されるコバルトの含有量を調整することで、硬度と靭性のバランスを最適化し、幅広い加工条件に対応することが可能です。また、断続切削や不安定な加工条件下でも安定した性能を発揮するため、多品種少量生産の現場で重宝されています。
K種
K種は鋳鉄用超硬合金として開発され、主にねずみ鋳鉄やダクタイル鋳鉄の加工に使用されます。
タングステンカーバイドを主成分とし、他の炭化物をほとんど含まないシンプルな組成が特徴です。この組成により、非常に高い硬度と優れた耐摩耗性を実現し、鋳鉄特有の硬い黒鉛組織を含む材料の加工に最適な性能を発揮します。
特に切れ味が良く、低い切削抵抗で加工できるため、鋳造部品の仕上げ加工や大量生産ラインでの連続加工に適しています。近年は自動車のブレーキディスクやエンジンブロックなどの加工にも広く使用されています。
超硬合金のメリット
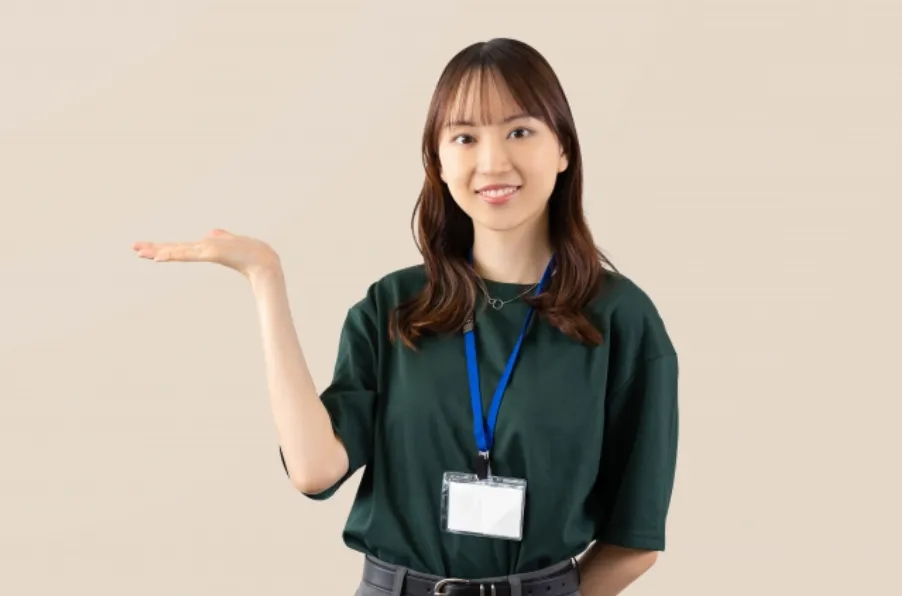
超硬合金は、その優れた物理的特性から、製造業に多大な恩恵をもたらしています。特に、耐久性の向上とコスト削減、環境負荷の低減などです。また、加工精度の向上により、より精密な製品製造を可能にしています。
ここでは、超硬合金を使用することで得られる具体的なメリットについて、実例を交えながら解説していきます。
リサイクルできる
超硬合金の重要なメリットの一つが、リサイクル可能な素材であることです。
主成分のタングステンは希少金属であり、その産出は特定の地域に偏在しています。しかし、超硬合金は適切な回収システムにより、高い割合で再利用が可能です。使用済みの超硬工具や金型は、粉砕・分離工程を経て新たな超硬合金の原料として生まれ変わります。
このリサイクルシステムにより、資源の有効活用が進み、環境負荷の低減とコスト削減を同時に実現しています。また、原材料の安定供給にも貢献し、製造業の持続可能性を高めることにもつながっているといえるでしょう。
寿命が長くなる
超硬合金を使用した工具や部品は、従来の鋼材と比較して圧倒的に長い寿命を誇ります。
例えば、切削工具の場合、一般的な高速度鋼と比べて寿命が長くなります。これは、高い硬度と耐摩耗性、そして高温での性能維持能力によるものです。工具の交換頻度が大幅に減少することで、生産ラインの停止時間が短縮され、生産効率が向上します。
また、工具費用の削減だけでなく、交換作業に関わる人件費や在庫管理コストも低減できます。さらに、安定した工具寿命により、加工品質のばらつきも抑制され、製品の歩留まり向上にも効果的です。
加工精度が上がる
超硬合金の使用により、加工精度は飛躍的に向上します。
従来の工具鋼と比較して、変形が少なく、熱による寸法変化も最小限に抑えられるため、ミクロン単位の精密加工が可能です。特に、電子部品や医療機器部品など、高い寸法精度が要求される製品の製造において、その効果は顕著です。また、工具の摩耗が少ないため、長時間の加工でも安定した精度を維持できます。
さらに、硬度が高いことで切れ味が良く、加工面の品質の向上が可能です。これにより、後工程の仕上げ加工を省略できるケースも多く、生産効率の向上にもつながっています。
超硬合金の弱点・デメリット
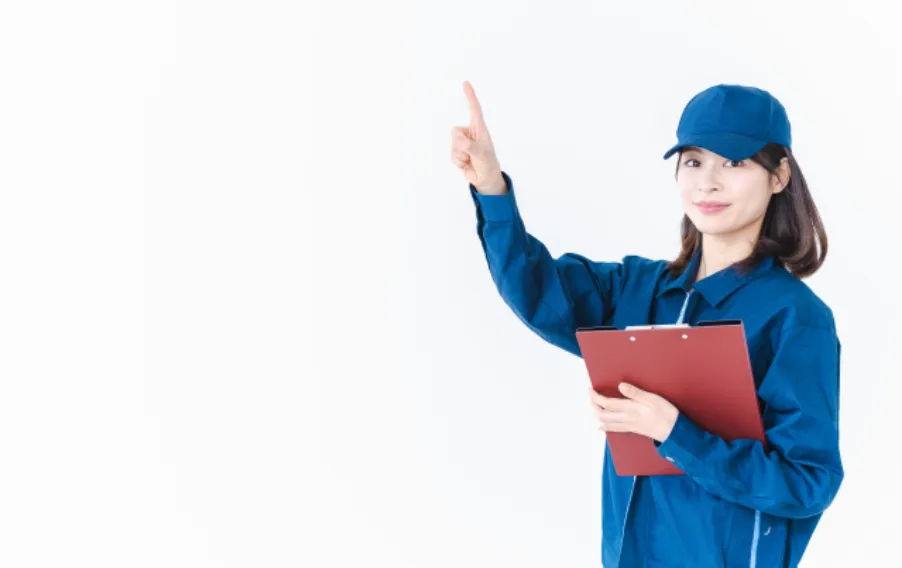
超硬合金は優れた特性を持つ一方で、いくつかの課題も抱えています。特に、その重量と脆性という二つの特性は、使用時に考慮すべき重要な要素です。また、製造コストの高さも無視できない問題です。
ここでは、超硬合金の持つ弱点について、その対策方法も含めて詳しく解説していきます。
重い
超硬合金の密度は鉄の約2倍にも及び、この重さは様々な場面で課題になるでしょう。
例えば、ハンドツールとして使用する場合、作業者の疲労増加につながり、長時間の使用が困難になることがあります。また、高速回転する工作機械のツーリングでは、バランスの調整が重要になり、設計時に特別な配慮が必要です。大型の金型や工具では、重量制限のある設備での使用が制限されたり、運搬・設置に特殊な機器が必要になったりすることもあります。
これらの問題に対しては、必要な部分のみに超硬合金を使用するなど、設計上の工夫が求められています。
刃先が欠けやすい
超硬合金は高い硬度を持つ反面、衝撃に対して弱い性質があります。
特に刃先や角部では、急激な負荷がかかると欠けや割れが発生しやすく、これは工具寿命を大きく左右する要因といえるでしょう。例えば、断続切削や不安定な加工条件下では、チッピングと呼ばれる微細な欠けが発生しやすく、これが進行すると工具の破損につながります。また、取り扱い時の落下や接触による損傷も起こりやすいため、保管や運搬時には細心の注意が必要です。
これらの問題に対しては、適切な使用条件の設定や、耐衝撃性を高めた材種の選択が重要です。
超硬合金の活用方法
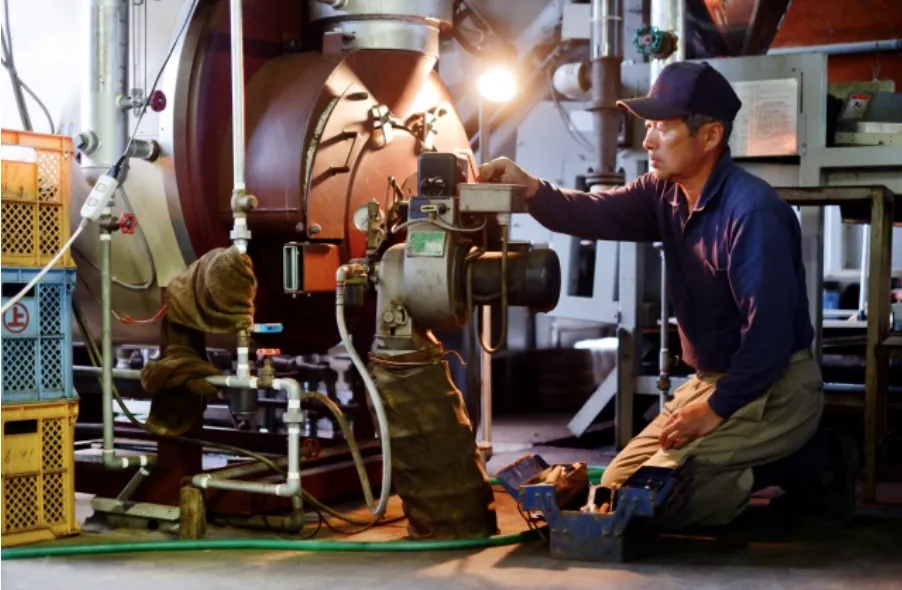
超硬合金は、その優れた特性から製造業の様々な場面で活用されています。特に金属加工の分野では必要不可欠な存在となり、また建設・土木分野でも重要な役割を果たしています。
ここでは、産業界における超硬合金の具体的な活用方法について、実例を交えながら詳しく解説していきます。生産性向上や品質改善にどのように貢献しているのかを見ていきましょう。
金属部品の加工
金属部品の加工分野では、超硬合金製の工具が幅広く活用されています。
特に自動車産業では、エンジン部品やトランスミッション部品の製造に不可欠です。例えば、高精度な穴あけが必要なインジェクターノズルの加工では、超硬ドリルが使用されます。また、半導体製造装置の部品加工でも、その高い精度と安定性が重要視されています。超硬工具を使用することで、加工時間の短縮と品質の向上を同時に実現できるでしょう。
さらに、航空機部品の製造では、チタン合金などの難削材加工に超硬工具が必須とされ、高い生産性と信頼性を確保しています。
切削・掘削
建設・土木分野では、超硬合金の耐摩耗性を活かした切削・掘削工具が重要な役割を果たしています。
例えば、トンネル掘削機のカッタービットには超硬合金が使用され、硬い岩盤でも効率的な掘削を可能に。また、道路工事で使用されるアスファルトカッターの刃先にも採用され、長時間の連続作業が可能です。鉱山での採掘作業においても、超硬製のドリルビットが活躍し、作業効率の向上に貢献しています。
これらの用途では、工具の長寿命化により、作業の中断回数を減らし、工期短縮とコスト削減を実現しています。
まとめ
超硬合金は、その高い硬度と耐摩耗性により、現代の製造業になくてはならない素材です。確かに重量や脆性など、いくつかの課題はありますが、適切な使用方法と材種選択により、それらを最小限に抑えられます。今後も新しい組成や製造方法の研究が進み、さらなる性能向上が期待される材料といえるでしょう。産業界の発展とともに、超硬合金の重要性は一層高まっていくことでしょう。